Difference between revisions of "Three-speaker Chladni Patterns"
Anup Tapase (talk | contribs) |
Lingyu Xie (talk | contribs) |
||
(22 intermediate revisions by 2 users not shown) | |||
Line 1: | Line 1: | ||
[[Image: |
[[Image:chladni_complete_system|right|Three-Speaker Chladni Setup with User Interface Box|thumb|500px]] |
||
⚫ | |||
== Team Members == |
== Team Members == |
||
[[image:chladni_team|right]] |
[[image:chladni_team|right]] |
||
Line 10: | Line 11: | ||
== Overview == |
== Overview == |
||
The purpose of this project was to build on the past projects that have been seen on Youtube and other sites involving vibrating a metal plate using one speaker or violin bow. This project uses three speakers separated by 120 degrees which vibrate a circular plate to generate patterns with salt. These patterns are created because when the speakers hit the resonant frequency of the plate, nodes are created on the plate and the salt migrates to these nodes because they are vibrating the least. The project also includes a user interface which the user can use to select different patterns or frequencies for the plate. |
The purpose of this project was to build on the past projects that have been seen on Youtube and other sites involving vibrating a metal plate using one speaker or violin bow. This project uses three speakers separated by 120 degrees which vibrate a circular plate to generate patterns with salt. These patterns are created because when the speakers hit the resonant frequency of the plate, nodes are created on the plate and the salt migrates to these nodes because they are vibrating the least. The project also includes a user interface which the user can use to select different patterns or frequencies for the plate. |
||
<br> |
|||
<br> |
|||
== Theory == |
== Theory == |
||
As explained in the overview, the Chladni plate generates patterns when the frequency of the plate oscillation is at a resonant frequency for the plate. At resonance, the plate has portions where it has non-zero amplitude during oscillation, which is where the salt moves away from toward areas of zero amplitude. Areas of zero amplitude are called nodes or zeros of vibration, and salt collects at these regions on the plate at resonance. The nodes of vibration of a circular or square plate can be mathematically calculated for different modes of vibration. The following paragraphs summarize the equations that can be used to determine the shapes of nodes or the frequencies that cause the nodes, but additional websites such as [http://local.wasp.uwa.edu.au/~pbourke/geometry/chladni/ Chladni Plate Mathematics] and [http://webphysics.davidson.edu/alumni/jimn/Java/modes.html Chladni Figures and Vibrating Plates] can be used to visualize the different modes of square and circular plates better.<br> |
As explained in the overview, the Chladni plate generates patterns when the frequency of the plate oscillation is at a resonant frequency for the plate. At resonance, the plate has portions where it has non-zero amplitude during oscillation, which is where the salt moves away from toward areas of zero amplitude. Areas of zero amplitude are called nodes or zeros of vibration, and salt collects at these regions on the plate at resonance. The nodes of vibration of a circular or square plate can be mathematically calculated for different modes of vibration. The following paragraphs summarize the equations that can be used to determine the shapes of nodes or the frequencies that cause the nodes, but additional websites such as [http://local.wasp.uwa.edu.au/~pbourke/geometry/chladni/ Chladni Plate Mathematics] and [http://webphysics.davidson.edu/alumni/jimn/Java/modes.html Chladni Figures and Vibrating Plates] can be used to visualize the different modes of square and circular plates better.<br> |
||
Line 20: | Line 23: | ||
The following equation is Chladni's Law: [[image:chladnis_law]]. This equation relates the modes of vibration to the frequency of the modes for circular plates with a fixed center, similar to the one used by our three-speaker system except that our plate is fixed at three points away from the center. In the equation, C and p are defined based on the properties of the plate. For circular plates, p is approximately 2. The values of m and n are chosen based on the diametric and radial modes which can be determined by the shapes of the nodes on the plate, then converted to the frequency of the plate that made that shape.<br> |
The following equation is Chladni's Law: [[image:chladnis_law]]. This equation relates the modes of vibration to the frequency of the modes for circular plates with a fixed center, similar to the one used by our three-speaker system except that our plate is fixed at three points away from the center. In the equation, C and p are defined based on the properties of the plate. For circular plates, p is approximately 2. The values of m and n are chosen based on the diametric and radial modes which can be determined by the shapes of the nodes on the plate, then converted to the frequency of the plate that made that shape.<br> |
||
<br> |
|||
== Mechanical Design == |
== Mechanical Design == |
||
Line 95: | Line 99: | ||
<br clear=all> |
<br clear=all> |
||
<br> |
|||
== Electrical Design == |
== Electrical Design == |
||
Line 132: | Line 137: | ||
For easier and more convenient use, sockets were made for header pins from the power supplies, potentiometer, RCA input cables and the parallel LCD. This way, the components can be plugged in and out easily. |
For easier and more convenient use, sockets were made for header pins from the power supplies, potentiometer, RCA input cables and the parallel LCD. This way, the components can be plugged in and out easily. |
||
The TDA2040 audio amplifier chip was first used instead of the car audio amplifier. This chip draws a lot of power, and to amplify three speakers, three chips were needed that drew 24V each. Results with these were inconsistent and hence the car audio amplifier was used instead. The circuit diagram for this chip is shown below |
The TDA2040 audio amplifier chip was first used instead of the car audio amplifier. This chip draws a lot of power, and to amplify three speakers, three chips were needed that drew 24V each. Results with these were inconsistent and hence the car audio amplifier was used instead. The circuit diagram for this chip is shown below as well. |
||
Also, using three separate function generator chips for each speaker was unfruitful. The fragility of the chips as well as the difficulty in transferring three different signals through SPI led us to resort to using only one of them. |
Also, using three separate function generator chips for each speaker was unfruitful. The fragility of the chips as well as the difficulty in transferring three different signals through SPI led us to resort to using only one of them. |
||
=== Circuit Diagram === |
=== Circuit Diagram === |
||
<br clear=all> |
<br clear=all> |
||
[[image:chladni_circuit_actual|Circuit schematic of circuit used for demonstration 3-speaker Chladni|thumb|500px]] |
[[image:chladni_circuit_actual|left|Circuit schematic of circuit used for demonstration 3-speaker Chladni|thumb|500px]] |
||
⚫ | |||
<br clear=all> |
|||
Note: If the TDA2040 is to be used, connect the output of the unity gain buffer amps to the Vi input of the TDA2040 chip. The load at pin 4 of the TDA2040 chip is then the speaker. +Vs is +12V and -Vs is -12V for the TDA2040 circuit. |
|||
<br clear=all> |
<br clear=all> |
||
⚫ | |||
⚫ | |||
<br><br><br><br><br><br><br><br><br><br><br><br><br><br><br> |
|||
== Code == |
== Code == |
||
Line 154: | Line 157: | ||
After this, the analog port pin is set up and the lcd_init() function is called to set up the LCD display. The LCD displays the current frequency that the AD9833 is currently outputting and the target frequency that the chip is supposed to sweep up/down to. See [[C Example: Parallel Interfacing with LCDs]] to learn about how to interface and send information to the LCD. |
After this, the analog port pin is set up and the lcd_init() function is called to set up the LCD display. The LCD displays the current frequency that the AD9833 is currently outputting and the target frequency that the chip is supposed to sweep up/down to. See [[C Example: Parallel Interfacing with LCDs]] to learn about how to interface and send information to the LCD. |
||
Once the initial set up information is finished, the code sends the first frequency command to the AD9833, starting it at a frequency of 298 Hz by giving it the target_freq_reg register value (initialized at 298 Hz). This allows the speakers to sweep up to the first resonant frequency and oscillate the salt into the first resonant shape when the system is turned on. The register values are then converted to Hz and displayed on the LCD. From there, the code goes into a while() loop which continuously checks the input from the user interface knob which indicates the target frequency that the AD9833 should go to. After getting the target frequency from check_input(), the code compares this new frequency information to the old frequency information (old_freq_reg). If they are different, then the knob was switched to a new frequency and the AD9833 needs to sweep up or down to the new frequency. Depending on whether the new frequency is above or below the old frequency, a for-loop will keep sending new frequency register commands to the AD9833, |
Once the initial set up information is finished, the code sends the first frequency command to the AD9833, starting it at a frequency of 298 Hz by giving it the target_freq_reg register value (initialized at 298 Hz). This allows the speakers to sweep up to the first resonant frequency and oscillate the salt into the first resonant shape when the system is turned on. The register values are then converted to Hz and displayed on the LCD. From there, the code goes into a while() loop which continuously checks the input from the user interface knob which indicates the target frequency that the AD9833 should go to. After getting the target frequency from check_input(), the code compares this new frequency information to the old frequency information (old_freq_reg). If they are different, then the knob was switched to a new frequency and the AD9833 needs to sweep up or down to the new frequency. Depending on whether the new frequency is above or below the old frequency, a for-loop will keep sending new frequency register commands to the AD9833 by calling send_freq(), which is a function that shifts the frequency up or down by 1 Hz every 100 ms, and constantly updates the LCD to display the current and target frequency until the actual frequency is equal to the target frequency. The function check_input() is called for each iteration of the for-loop to check if the target frequency was changed. The old_target_freq_reg is then set equal to the target_freq_reg and the program then holds at this one resonant frequency until the knob sends a different target_freq_reg. |
||
<pre> |
<pre> |
||
Line 173: | Line 176: | ||
void check_input(); |
void check_input(); |
||
void send_freq(int16 f_reg); |
|||
void main() |
void main() |
||
Line 213: | Line 217: | ||
for(ct=old_target_freq_reg; ct<=target_freq_reg; ct=ct+7) //ct+7 approximate increases frequency by 1 Hz |
for(ct=old_target_freq_reg; ct<=target_freq_reg; ct=ct+7) //ct+7 approximate increases frequency by 1 Hz |
||
{ |
{ |
||
send_freq(ct); //send frequency to chip and display status on LCD |
|||
⚫ | |||
⚫ | |||
⚫ | |||
⚫ | |||
⚫ | |||
⚫ | |||
target_freq=(float).149011 * (float)(target_freq_reg - 16384); |
|||
⚫ | |||
⚫ | |||
check_input(); //see if knob position has selected different target freq |
check_input(); //see if knob position has selected different target freq |
||
Line 239: | Line 230: | ||
for(ct=old_target_freq_reg; ct>=target_freq_reg; ct=ct-7) //ct+7 approximate decreases frequency by 1 Hz |
for(ct=old_target_freq_reg; ct>=target_freq_reg; ct=ct-7) //ct+7 approximate decreases frequency by 1 Hz |
||
{ |
{ |
||
send_freq(ct); //send frequency to chip and display status on LCD |
|||
spi_xfer(0b0010000100000000); |
|||
spi_xfer(ct); //set AD9833 frequency to ct, which is freq register that is sweeping down by 7 each time loop is run |
|||
spi_xfer(0b0100000000000000); |
|||
spi_xfer(0b1100000000000000); |
|||
spi_xfer(0b0000000000000000); |
|||
⚫ | |||
target_freq=(float).149011 * (float)(target_freq_reg - 16384); //convert target freq register to target freq value |
|||
printf(lcd_putc,"\fFreq: %Lu Hz\n",freq); //display current freq |
|||
printf(lcd_putc,"Target: %Lu Hz\n",target_freq); //display target freq |
|||
check_input(); //see if knob position has selected different target freq |
check_input(); //see if knob position has selected different target freq |
||
Line 263: | Line 240: | ||
} |
} |
||
} |
} |
||
} |
|||
void send_freq(int16 f_reg) //send frequency from f_reg to AD9833 chip and display frequencies on LCD |
|||
{ |
|||
⚫ | |||
⚫ | |||
⚫ | |||
⚫ | |||
⚫ | |||
⚫ | |||
⚫ | |||
⚫ | |||
⚫ | |||
} |
} |
||
</pre> |
</pre> |
||
<br> |
|||
⚫ | |||
⚫ | |||
This function is used to check the knob/potentiometer position at certain points during the changing of frequencies in the main function. It sets the ADC channel to 0 and takes the analog input from pin A0 on the PIC using read_adc(). This input, set to the variable knob_val, is an integer between 0-255 which corresponds to the voltage coming out of the knob/potentiometer, which is 0 if the output is at 0V and 255 if the output is at 5V. By checking if knob_val is between a certain integer range corresponding to the different numbers on the knob (numbered 0-10), the target frequency can be set by the user. Nine target resonant frequencies were programmed in this function based on the good clarity of the shapes they produced on the plate, but more resonant frequencies exist and can be added to the if-statement in this function. The target frequency registers should be adjusted depending on the plate shape and size. |
This function is used to check the knob/potentiometer position at certain points during the changing of frequencies in the main function. It sets the ADC channel to 0 and takes the analog input from pin A0 on the PIC using read_adc(). This input, set to the variable knob_val, is an integer between 0-255 which corresponds to the voltage coming out of the knob/potentiometer, which is 0 if the output is at 0V and 255 if the output is at 5V. By checking if knob_val is between a certain integer range corresponding to the different numbers on the knob (numbered 0-10), the target frequency can be set by the user. Nine target resonant frequencies were programmed in this function based on the good clarity of the shapes they produced on the plate, but more resonant frequencies exist and can be added to the if-statement in this function. The target frequency registers should be adjusted depending on the plate shape and size. |
||
Line 356: | Line 353: | ||
For the purposes of demonstration we decided to use the LA160 car amp for a much cleaner signal and far more defined Chladni patterns. |
For the purposes of demonstration we decided to use the LA160 car amp for a much cleaner signal and far more defined Chladni patterns. |
||
<br><br> |
<br><br><br><br> |
||
== Possible Future Improvements/Enhancements == |
== Possible Future Improvements/Enhancements == |
||
Line 366: | Line 363: | ||
== References == |
== References == |
||
[http://local.wasp.uwa.edu.au/~pbourke/geometry/chladni/ Chladni Plate Mathematics]<br> |
* [http://local.wasp.uwa.edu.au/~pbourke/geometry/chladni/ Chladni Plate Mathematics]<br> |
||
[http://en.wikipedia.org/wiki/Chladni's_law Chladni's Law]<br> |
* [http://en.wikipedia.org/wiki/Chladni's_law Chladni's Law]<br> |
||
[http://www.phy.davidson.edu/StuHome/derekk/Chladni/pages/menu.htm A study of vibrating plates]<br> |
* [http://www.phy.davidson.edu/StuHome/derekk/Chladni/pages/menu.htm A study of vibrating plates]<br> |
Latest revision as of 01:38, 20 March 2009
Team Members
- Christopher Chow (Mechanical Engineering, Class of 2010)
- Anup Tapase (Electrical Engineering, Class of 2010)
- Lingyu Xie (Electrical Engineering, Class of 2009)
Overview
The purpose of this project was to build on the past projects that have been seen on Youtube and other sites involving vibrating a metal plate using one speaker or violin bow. This project uses three speakers separated by 120 degrees which vibrate a circular plate to generate patterns with salt. These patterns are created because when the speakers hit the resonant frequency of the plate, nodes are created on the plate and the salt migrates to these nodes because they are vibrating the least. The project also includes a user interface which the user can use to select different patterns or frequencies for the plate.
Theory
As explained in the overview, the Chladni plate generates patterns when the frequency of the plate oscillation is at a resonant frequency for the plate. At resonance, the plate has portions where it has non-zero amplitude during oscillation, which is where the salt moves away from toward areas of zero amplitude. Areas of zero amplitude are called nodes or zeros of vibration, and salt collects at these regions on the plate at resonance. The nodes of vibration of a circular or square plate can be mathematically calculated for different modes of vibration. The following paragraphs summarize the equations that can be used to determine the shapes of nodes or the frequencies that cause the nodes, but additional websites such as Chladni Plate Mathematics and Chladni Figures and Vibrating Plates can be used to visualize the different modes of square and circular plates better.
The equation solves for the zeros of the standing wave for a square plate constrained at the center, such as the one we used for our one-speaker configuration. The variable L is the side length of the plate, m is the number of diametric nodes and n is the number of radial nodes.
The equation to find the zeros for a circular plate is . The Jn(K*r) term is using the n-th order Bessel function.
The following equation is Chladni's Law: . This equation relates the modes of vibration to the frequency of the modes for circular plates with a fixed center, similar to the one used by our three-speaker system except that our plate is fixed at three points away from the center. In the equation, C and p are defined based on the properties of the plate. For circular plates, p is approximately 2. The values of m and n are chosen based on the diametric and radial modes which can be determined by the shapes of the nodes on the plate, then converted to the frequency of the plate that made that shape.
Mechanical Design
The Chladni pattern generator setup is pretty straightforward. There were three major areas of design we had to account for. One was how to adapt the speakers to attach to the metal plate, the second was the speaker housing, and the third was the user interface/circuit box. These are detailed with pictures below.
If you are trying to replicate this project, note that many of these specifications can change and still yield interesting, but different results. Another thing to note is all the specifications are for our particular speakers. Dimensions and materials can change according to what you're working with and what is available.
Parts List
The parts and prices below are specific to the project we did. You can change many of the parts to suit different components. We were fortunate to have most of the materials in supply so we could save money for the aluminum plate and electronics.
Part | Part No. | Qty | Vendor | Price (Total) |
---|---|---|---|---|
PYRAMID 8" Originals 300W | WX85 | 3 | Lab | - |
AL 6061) .032" THICK, 36"X36" | 89015K71 | 1 | McMaster | $53.23 |
Wood stock | - | ~40"X40" | Shop supply | - |
Polystyrene Sheets | - | ~20"X40" | Shop supply | - |
PVC tube 1.5" Dia | - | ~ 1 ft | Shop supply | - |
Polycarbonate sheet | - | ~6"X6" | Shop supply | - |
Nuts, Bolts, Washers | - | ~20 | Shop supply | - |
Foamcore | - | 2 Sheets 36"X28" | EDC Supply | - |
L Brackets | - | ~20 | Shop supply | - |
Breakdown of Components
Adapting Speakers
- First we cut away the dust-cap as pictured to the right
- Glued onto the diaphragm of the speaker and over the dustcap is a 2 inch long PVC pipe that covers the hole.
- Over the PVC pipe we glued a 2" x 2" piece of polycarbonate.
- We screwed a hole into the center of the polycarbonate and put in a screw.
- The screw is fastened with nuts and washers. The flexible aluminum plate will ultimately be attached to the speaker through this screw.
For more information on how speakers work, click here.
Speaker-boxes and Base
- Cut a hole into the top of the speaker box to seat the speaker.
- We planned the base so that the speakers would be radially separated by 120 degrees and the centers of each speaker to create a 13" equilateral triangle with each other.
- We lined the bottoms of the speaker boxes and the base with Velcro for convenience and accessibility.
- The speaker set up sits in a 32" x 32" foamcore box reinforced with L-brackets. This is to catch the salt that spills off of the aluminum plate.
User Interface and Circuit Box
- A simple box with a hinged top that can be made out of anything, we chose to use a black Polystyrene material that was available.
- The user interface panel needs to have slots cut for the two power switches, and LCD screen, and a knob. The laser printer and mill were both used to make these cutouts.
Putting it Together
- The last piece needed is a metal plate. We cut down the 36" x 36" aluminum plate into a 28" diameter circular plate.
- Pictured to the side is the complete set up.
Electrical Design
Primary Components
The primary components required to implement the circuit include:
Part | Part No. | Qty | Vendor | Price (Total) |
---|---|---|---|---|
PIC Microcontroller | PIC18F4520 | 1 | Lab | - |
Function generator chip (surface mount) | AD9833 BRMZ-ND | 1 | Digi-Key | $9.42 |
10-Pin Adaptor for surface mount | 33010CA-ND | 1 | Digi-Key | $3.22 |
General Purpose Op-Amp | LM741 | 3 | Lab | - |
Parallel LCD | JHD 162A | 1 | Lab | - |
Audio amplifier chip | TDA2040 | 3 | Lab | - |
Car audio amplifier (at least 3 channel) | Legacy LA160 | 1 | Lab | - |
Circuit Notes
The PIC communicates with the AD9833 function generator chip through SPI interface. Refer to Waveform Generation with AD9833, and SPI for how to use this chip. The Master Clock is connected to the CLK of the PIC, and the three SPI communication lines are connected to the three I/O pins A1, A2 and A3 on the PIC. Through the code described below via SPI, information about the wave to be generated is transmitted and the function wave is generated accordingly.
A 10K potentiometer is used as input from the user in the form of a knob to set the frequency. It is connected to pin A0 of the PIC, and its use is described in detail under the Code section.
The output of the AD9833 chip is connected to the non-inverting inputs of three LM741 Op Amps. These op-amps are not used to amplify the signal, but to serve as a unity gain buffer for the signals. They are connected to a +/- 12V power supply. This buffer essentially makes a copy of the input at the output, without drawing any current from the source of the input, i.e., the function generator chip, which gets its power from the PIC supply. Instead, the output signal draws power from the op-amp itself. The goal is to ensure that doing the measurement of a voltage does not disturb the circuit producing the voltage to be measured.
The outputs of the op-amps are then connected to the car amplifier using standard RCA input cables. The car amplifier, which is connected to a 12V supply, amplifies the signal to audible amplitudes and the outputs are connected to the three speakers. The speakers draw power from the car amplifier.
The D0-D6 outputs of the PIC are connected to the Parallel LCD. To learn more about how to get the LCD working, refer to C Example: Parallel Interfacing with LCDs. The LCD is made to display the target frequency that the user inputs using the knob (which is on the potentiometer), and also the value of the frequency of the wave that is being generated at the moment.
For easier and more convenient use, sockets were made for header pins from the power supplies, potentiometer, RCA input cables and the parallel LCD. This way, the components can be plugged in and out easily.
The TDA2040 audio amplifier chip was first used instead of the car audio amplifier. This chip draws a lot of power, and to amplify three speakers, three chips were needed that drew 24V each. Results with these were inconsistent and hence the car audio amplifier was used instead. The circuit diagram for this chip is shown below as well.
Also, using three separate function generator chips for each speaker was unfruitful. The fragility of the chips as well as the difficulty in transferring three different signals through SPI led us to resort to using only one of them.
Circuit Diagram
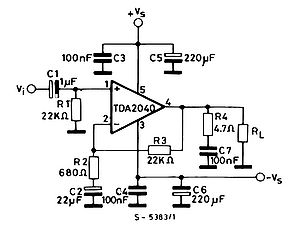
Note: If the TDA2040 is to be used, connect the output of the unity gain buffer amps to the Vi input of the TDA2040 chip. The load at pin 4 of the TDA2040 chip is then the speaker. +Vs is +12V and -Vs is -12V for the TDA2040 circuit.
Code
Main frequency sweep code
The first thing that this code does is that it initializes the variables target_freq_reg and old_target_freq_reg to the register value of 298 Hz, which is a non-resonant frequency. See Waveform_Generation_with_AD9833,_and_SPI to find out how to convert between frequency and register value for commands sent to the AD9833 function generator chip, and sending commands to the AD9833 using SPI. After this, the analog port pin is set up and the lcd_init() function is called to set up the LCD display. The LCD displays the current frequency that the AD9833 is currently outputting and the target frequency that the chip is supposed to sweep up/down to. See C Example: Parallel Interfacing with LCDs to learn about how to interface and send information to the LCD.
Once the initial set up information is finished, the code sends the first frequency command to the AD9833, starting it at a frequency of 298 Hz by giving it the target_freq_reg register value (initialized at 298 Hz). This allows the speakers to sweep up to the first resonant frequency and oscillate the salt into the first resonant shape when the system is turned on. The register values are then converted to Hz and displayed on the LCD. From there, the code goes into a while() loop which continuously checks the input from the user interface knob which indicates the target frequency that the AD9833 should go to. After getting the target frequency from check_input(), the code compares this new frequency information to the old frequency information (old_freq_reg). If they are different, then the knob was switched to a new frequency and the AD9833 needs to sweep up or down to the new frequency. Depending on whether the new frequency is above or below the old frequency, a for-loop will keep sending new frequency register commands to the AD9833 by calling send_freq(), which is a function that shifts the frequency up or down by 1 Hz every 100 ms, and constantly updates the LCD to display the current and target frequency until the actual frequency is equal to the target frequency. The function check_input() is called for each iteration of the for-loop to check if the target frequency was changed. The old_target_freq_reg is then set equal to the target_freq_reg and the program then holds at this one resonant frequency until the knob sends a different target_freq_reg.
/* Chladni Code Lingyu Xie, Anup Tapase, Chris Chow ME333 Winter 2009 */ #include <18f4520.h> #DEVICE ADC=8 // set ADC to 8 bit accuracy #use delay(clock=40000000) #include "flex_lcd.c" //must include in order to output to LCD #use spi(DO = PIN_A3, CLK = PIN_A2, ENABLE = PIN_A1, BITS = 16, MASTER, ENABLE_ACTIVE = 0, MSB_FIRST, IDLE = 1) int16 freq,target_freq; int16 target_freq_reg, old_target_freq_reg; int8 knob_val=0; void check_input(); void send_freq(int16 f_reg); void main() { int16 ct; target_freq_reg=2000+16384; // initialize starting frequency of speakers to 298 Hz (non-resonant) old_target_freq_reg=2000+16384; // set old target freq variable to equal target freq setup_adc_ports(AN0); // Set up analog input port as pin A0 setup_adc(ADC_CLOCK_INTERNAL); lcd_init(); // Always call this first. //INITIAL FREQUENCY FOR AD9833 spi_xfer(0b0010000100000000); //format command, output sine wave spi_xfer(target_freq_reg); //1st set of bits, 14 LSB, this range is good enough for our use //send the target frequency register value (freq + 16384) to AD9833 chip spi_xfer(0b0100000000000000); //2nd set of bits, 14 MSB spi_xfer(0b1100000000000000); //phase register: 0 phase shift (B0-B13) spi_xfer(0b0000000000000000); //unformat freq=(float).149011 * (float)(target_freq_reg - 16384); //convert the target freq register value to actual freq value target_freq=freq; // initialize target freq as current freq printf(lcd_putc,"\fFreq: %Lu Hz\n",freq); //display current freq printf(lcd_putc,"Target: %Lu H\n",target_freq); //display target freq while(TRUE) { check_input(); //check the knob input to see if target frequency has changed if(old_target_freq_reg != target_freq_reg) //go in here if target freq changed after calling check_input() { if(target_freq_reg > old_target_freq_reg) //sweep up to target freq { for(ct=old_target_freq_reg; ct<=target_freq_reg; ct=ct+7) //ct+7 approximate increases frequency by 1 Hz { send_freq(ct); //send frequency to chip and display status on LCD check_input(); //see if knob position has selected different target freq delay_ms(90); //delay to allow speakers to play freq for 90 ms + 10 ms (in check_input() function) } old_target_freq_reg = target_freq_reg; //reached target freq, set both variables equal until knob position changed } else if(target_freq_reg < old_target_freq_reg) //sweep down to target freq { for(ct=old_target_freq_reg; ct>=target_freq_reg; ct=ct-7) //ct+7 approximate decreases frequency by 1 Hz { send_freq(ct); //send frequency to chip and display status on LCD check_input(); //see if knob position has selected different target freq delay_ms(90); //delay to allow speakers to play freq for 90 ms + 10 ms (in check_input() function) } old_target_freq_reg = target_freq_reg; //reached target freq, set both variables equal until knob position changed } } } } void send_freq(int16 f_reg) //send frequency from f_reg to AD9833 chip and display frequencies on LCD { spi_xfer(0b0010000100000000); spi_xfer(f_reg); //set AD9833 frequency to f_reg, which is freq register that is sweeping up by 7 each time loop is run spi_xfer(0b0100000000000000); spi_xfer(0b1100000000000000); spi_xfer(0b0000000000000000); freq=(float).149011 * (float)(f_reg - 16384); //convert to actual Hz value of frequency target_freq=(float).149011 * (float)(target_freq_reg - 16384); printf(lcd_putc,"\fFreq: %Lu Hz\n",freq); //display current freq printf(lcd_putc,"Target: %Lu Hz\n",target_freq); //display target freq }
Checking user input
This function is used to check the knob/potentiometer position at certain points during the changing of frequencies in the main function. It sets the ADC channel to 0 and takes the analog input from pin A0 on the PIC using read_adc(). This input, set to the variable knob_val, is an integer between 0-255 which corresponds to the voltage coming out of the knob/potentiometer, which is 0 if the output is at 0V and 255 if the output is at 5V. By checking if knob_val is between a certain integer range corresponding to the different numbers on the knob (numbered 0-10), the target frequency can be set by the user. Nine target resonant frequencies were programmed in this function based on the good clarity of the shapes they produced on the plate, but more resonant frequencies exist and can be added to the if-statement in this function. The target frequency registers should be adjusted depending on the plate shape and size.
void check_input() //check knob position to see if target freq has changed { set_adc_channel(0); // Set the analog input channel to 0 delay_us(10); // wait 10uS for ADC to settle to a newly selected input knob_val = read_adc(); // Read in knob user input to tell speakers what resonant freq to sweep up to delay_ms(10); // delay 10 ms to allow reading of analog input //check and set target_freq_reg according to knob position (0-255 values split into 9 discrete levels) if (knob_val >= 0 && knob_val< 22 ) target_freq_reg = 2281+16384; //339 Hz else if(knob_val >= 22 && knob_val< 54) target_freq_reg = 3308+16384; //493 Hz else if(knob_val >= 54 && knob_val< 86) target_freq_reg = 3778+16384; //563 Hz else if(knob_val >= 86 && knob_val< 117) target_freq_reg = 3986+16384; //594 Hz else if(knob_val >= 117 && knob_val< 147) target_freq_reg = 4207+16384; //627 Hz else if(knob_val >= 147 && knob_val< 178) target_freq_reg = 4362+16384; //650 Hz else if(knob_val >= 178 && knob_val< 209) target_freq_reg = 5006+16384; //746 Hz else if(knob_val >= 209 && knob_val< 239) target_freq_reg = 5308+16384; //791 Hz else if(knob_val >= 239 && knob_val< 255) target_freq_reg = 5872+16384; //875 Hz }
Results
Three-Speaker Chladni
The following images show the results of the Three-Speaker Chladni system at six different resonant frequencies. Some of these frequencies have clearer patterns than others, such as 424 Hz, 554 Hz, and 660 Hz. The less-clear ones might be due to imperfections in the plate or the speakers not hitting the exact resonant frequency. Some frequencies shown in these results are different than the ones in the code displayed above. The ones displayed below were chosen for their clarity and contrast from each other because some frequencies in the displayed code do not shift in pattern as much.
Click here for a video of our Three-speaker Chladni setup
Three-Speaker Configuration at 339 Hz
424 Hz
554 Hz
632 Hz
660 Hz
734 Hz
One-Speaker Chladni
Click here for a video of our one-speaker Chladni setup
As you can see from the video, the one-speaker setup gives more distinct patterns than our three-speaker setup. This may be because there is no other interference with the vibration that more speakers connected to the same plate may cause. The patterns are all very different from each other, indicating the different diametric and radial modes of the square plate.
Experimental Notes
AD9833 Waveform Generator
While a tremendously versatile and useful chip, we found it extremely difficult to work with. The chip itself is very small and as mentioned above needs to be soldered to an adapter. Surface mount soldering this chip is not easy to do by hand and the connection may be weak even if you've tested with a multimeter. We even found that performance of the chip can be improved simply by putting pressure on the chip, such as using electrical tape to tape it down to the adapter. This shows how difficult making a solid connection can be. However, if working properly this chip can be very powerful.
SPI communication with multiple AD9833 chips
We had wanted to try to send three different frequencies, one to each speaker. This would require the use of three AD9833s, which we attempted to build a circuit for. From the example code we used and edited from the Waveform_Generation_with_AD9833,_and_SPI page, we saw that the PIC could only use one pin A3 (digital output) of the PIC for communication with the chip, while the other two pins A1 and A2 were used as Enable and CLK. We tried duplicating the SPI connections from the PIC to three AD9833s, using the same connections for each chip, but after programming the PIC and running the program, we saw that the AD9833 chips were not responding in the correct way. We thought that the issue may be that the AD9833s could not be programmed at the same time, so we tried another method. We used three 2-input AND gates and fed the CLK line as one input to each AND gate, with the other input being a switch from the PIC that would go high if that certain AD9833 was to be programmed. The other two PIC outputs Enable and Digital Output would still go to each AD9833. The output of each AND gate would feed into SCLK (pin 7) of the AD9833 and go low if the CLK was low and the switch was high, signaling that the AD9833 should be programmed (AD9833 is programmed with SCLK is low). The AD9833s would then be programmed in series, as the switch for the first AD9833 would go high, then the second switch would go high while the first went low, and so on. However, this method did not cause the AD9833s to be programmed/output a signal at all. In the end, we found that just using one SPI connection to one AD9833 gave the best frequency output, so we decided to split that signal into three and send them through unity gain buffers (preventing undesired loading or interference). The output of the buffers would be sent to the LA160 car audio amplifer.
Sending Different Frequencies to Different Speakers
This was difficult to experiment with because of our issues with SPI communication to separate AD9833 chips. However throughout the project we experienced times when the speakers were operating at different frequencies. From what we have seen all speakers must be operating at the same frequencies for any pattern to show. Whenever there was a phase issue or difference in frequency the plate would exhibit buckling behavior throwing the salt several inches into the air.
Aluminum Plate
When deciding how to space the speakers we had to consider the aluminum plate. Too far apart and a thin plate might sag in the middle, while too close together and the plate might sag around the edges. Sag would create artificial nodes and cause salt to accumulate in the wrong areas.
We decided early on to space the centers of the speakers 13" apart and began testing to see which size and shape plate would give us the least sag. Ultimately 28" diameter circle plate allowed us the largest possible plate - so we could have larger patterns - without the plate sagging around the edges or in the middle. We started with 36" x 36" plate and band sawed our circular plate out of it.
Also we noticed that our patterns did not have perfect radial symmetry. As the patterns rely heavily on the shape of the plate, imperfections in the plate can cause unsymmetrical patterns. In addition to a few small dents and scratches, band-sawing the circle out of the large plate yielded jagged and crooked edges at several points.
Amplifier Chips
At first we planned to use the TDA-2040 audio amp chips. Our original circuit is pictured to the right. When working with one speaker the TDA-2040 chip worked beautifully. It requires a lot of power - 24 volts - which was supplied using -12V to +12V. The one speaker video was actually done with the TDA-2040 audio amp chip.
The next step was to have a TDA-2040 amplify the other two speakers. Each of the audio amps would need 24 volts. When we added the other speakers we noticed that this caused all the speakers to experience a drop in amplitude. Providing each audio amp with its own 24 volt power supply only yielded marginal improvements. However the signal was still very inconsistent and noisy.
For the purposes of demonstration we decided to use the LA160 car amp for a much cleaner signal and far more defined Chladni patterns.
Possible Future Improvements/Enhancements
- Try sending different frequencies (by figuring out how to program multiple AD9833 chips with one PIC) to each speaker to see if they generate different patterns.
- Use different plate size or different amount of speakers. For example, use 4 speakers and a large square plate to change the types of visible shapes at resonance.
- Figure out the power issue with multiple TDA-2040 audio amp chips so the project wouldn't rely on the LA160 car amp.
- Use a more rigid plate or construct one with less defects in shape.